2016.09.20
以下2016年9月17日~18日に開催されたSSTRの様子です。
朝3時起床、諸々の準備をして4:50頃自宅を出発し、スタート位置の江ノ島港を目指します。
いつ雨が降り出してもおかしくない天気なため、あらかじめ合羽着用なのが残念。
早朝の空いた道路を快調に走り、日の出を少し過ぎた5:35頃江ノ島港に到着。
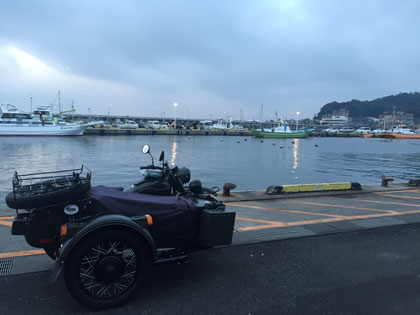
付近には他のSSTR参加者も集まっており、盛況の様子がうかがえますが何か様子がおかしい・・。
みんなスマホとにらめっこして出発する気配が無いのです。
自分も出発位置の登録のためスマホからシステムにアクセスすると、ログインすらままならない状態であることに気付きます。
まぁ、1800人のユーザーが数メガバイトの写真データを伴って一斉にアクセスするわけですからそうなるワナ。
何回試しても繋がらず、気付けば30分ほど経過してしまいました。
システムの利用を諦めてメールでスタートを申請して出発することにします、6時前には圏央道に上がり混む前に中央道に入る予定が狂ってしまったぜい。
おかげで圏央道に入る頃には高尾山から9km/45分の渋滞と出ています。
相模原ICで下道に降りて相模湖インターから中央道に乗るルートに変更することで渋滞をなんとか回避!
その後は混むこと無く進み、双葉SAで一回目の給油をして松本ICから「道の駅 風穴の里」までノンストップで到着。
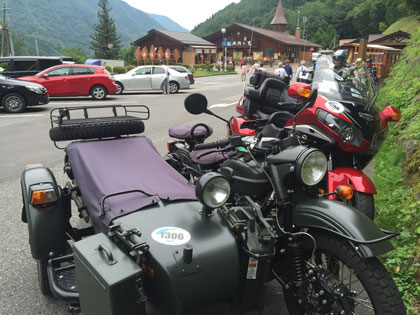
↑ チェックポイントでもある道の駅 風穴の里
わさび肉まんで小腹を満たしてR158を先に進みました。
安房トンネルを抜けてR471を神岡・富山方面へ下っていきます。
前後に車がいない状況がしばらく続き、ストレス無く走れてとても快適です。
途中、奥飛騨温泉郷上宝・宙ドーム神岡・細入と3つの道の駅に立ち寄ってポイントを獲得し、富山ICから北陸道に乗って距離を稼ぎます。
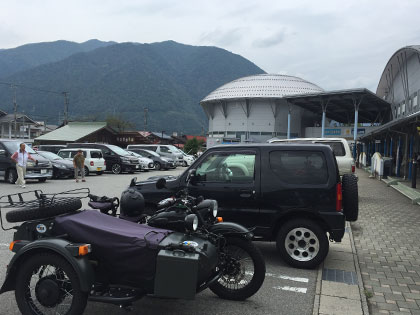
↑ 道の駅 宙ドーム神岡
砺波JCTから能越自動車道に分岐して氷見ICで降りて「道の駅 氷見」で軽く休憩。
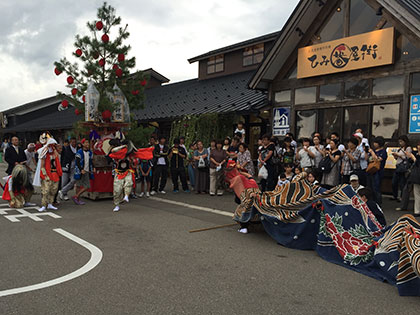
それから能登半島を西に向けて横断すること20kmぐらい。
14時過ぎにはゴール地点である羽咋に着いてしまいました。
実は羽咋のとある施設に訪問することがSSTR参加の動機であったため必要最低限のポイントにしか立ち寄らず、早めの到着を目指していたのです。
羽咋といえば「UFOの街」を観光アピールに利用しています。
駅前のUFOオブジェやゆるキャラ?のサンダー君など、なかなかのチカラの入れっぷり。
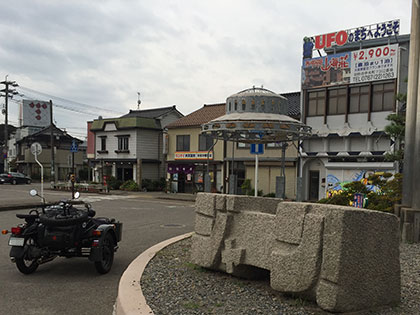
特に目的の施設「コスモアイル羽咋」はUFOファンならずとも一目おかれた存在です。
というのも、世界的にも貴重な宇宙機の実物が幾つか展示されており、間近に見学することが出来るからです。
自分もバイコヌールまでソユーズの打ち上げを見に行ったことがあるほどコアな宇宙クラスタの一員ですから、一度はこの施設に立ち寄りたいと思っていました。
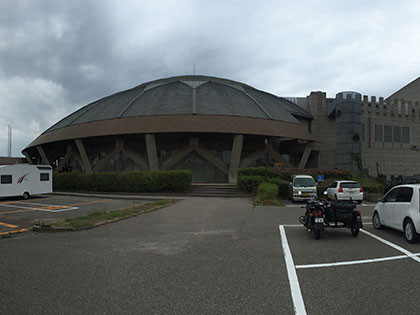
↑ コスモアイル羽咋
SSTR参加者は割引料金適用で少しお安く入場することが出来ます。
2階の展示場所は薄暗い照明の中、東西の宇宙機模型や実物が並んでいます。
ルナ計画のサンプルリターン機やモルニヤ衛星、ボストーク宇宙船など東側の宇宙機は実物が多く、興味のある人にとっては垂涎ものです。
↓ ルナ24号月面着陸船(旧ソ連製)
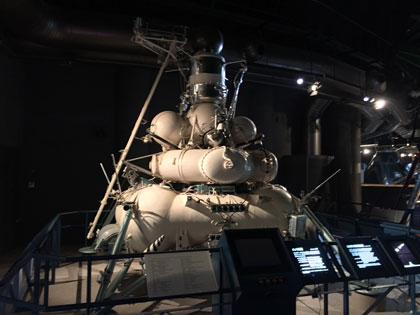
それらと一緒にUFOとか宇宙人の目撃情報などマユツバな展示も同一空間にあってなかなかカオスな空間となっています。
過去3度も羽咋に来ているのに、UFO関連の怪しさでなんとなくコスモアイルを敬遠しており、今回初めての訪問となったのでした。
ふたを開けてみればUFO含めて結構楽しめたので、もっと早く訪れれば良かったと反省。
このあと某SNSで知り合ったウラル仲間と隊列を組んでゴールする予定になっていたので、待ち合わせの「道の駅 高松」まで移動しました。
16:30千里浜に向けて隊列を組んで出発。
曇天で夕日の見えない砂浜を走り無事日没前にゴールを果たしたのでした。
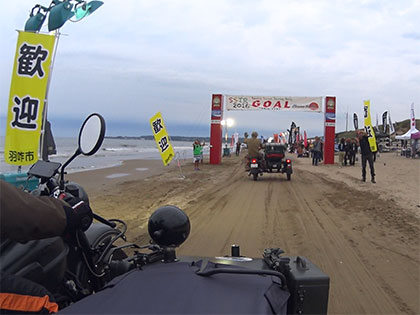
しかし、辛うじて持ちこたえていた天気も日没を迎えるとほぼ同時に崩れて雨が降り出してしまいました。
各々のウラルを肴にして談義に華を咲かせたかったのですが、早々に氷見のビジネスホテルに移動して一泊。
翌日のイベントにも参加せず、豪雨の中ただひたすら帰宅したのでした。
氷見→高山→安房→松本→中央道のルートで約10時間(内2時間はR16の渋滞でしたが...)、総走行距離898kmで無事帰宅。
五箇山辺りの高速道路では、対向車線を走る車が跳ね上げる水しぶきをさんざん浴びてもはや罰ゲームでした。
なんの修行なのかと笑いがこみ上げてくるほど。
そんなシビアコンディションでもウラルは絶好調でノートラブルでした、むしろ雨による強制水冷でオーバーヒート知らず?
↑ 全行程 ↓SSTR完走ピンズ
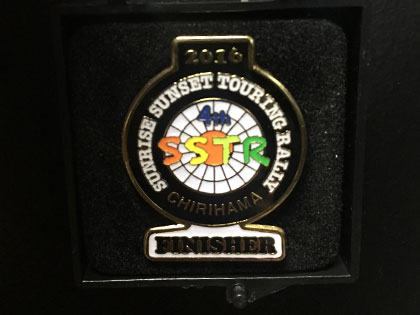